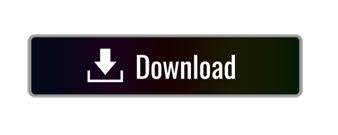

The latest industry news-straight to your inbox. You accept the use of cookies or other identifiers by closing or dismissing this notice, by scrolling this page, by clicking a link or button or by continuing to browse otherwise. To find out more about the categories of personal information collected and the purposes for which such information will be used, please refer to our privacy policy. In case of sale of your personal information, you may opt out by sending us an email via our Contact Us page. To learn more, please refer to the cookie policy. This website or its third-party tools process personal data e.
POST PROCESSOR MASTERCAM HOW TO
If we set up a job that had negative X or Y values, the machine would soft error out very quickly once it hit those lines, as it would hit it's built-in limits for when it's at that corner it's already almost at the end of it's travel.Pb_user_ / Octo/ How to make post processor for mastercam / commentsįorum Rules. For example, with our router, we're used to working with the bottom left corner of the table as our X and Y zero, and then having everything be positive values from there. If you go into the Tables screen on the controller you can see where the G54 offset values are and edit them to whatever it is you expected them to be. It's probably not where you expected it to be, or wanted it to be. So in other words, if now you were to enter in X0, and then Y0, you'd see where the G54 offset 'home' was set on your machine. Then switch to MDI mode, enter in G54, and execute, and you should see your axis value readout change from the 0,0,0 to whatever the negative of your G54 offset is.
POST PROCESSOR MASTERCAM CODE
The problem could be that whatever values stored in your G54 table don't align with what you've got setup in your Inventor job and/or post processor.įor example, we were hitting this same issue until we realized that the values entered in for the G54 offset weren't in alignment with how we are used to working in our CAM software.Īn easy test for this is put the machine in a MDI mode, where you can just enter in G code directly.
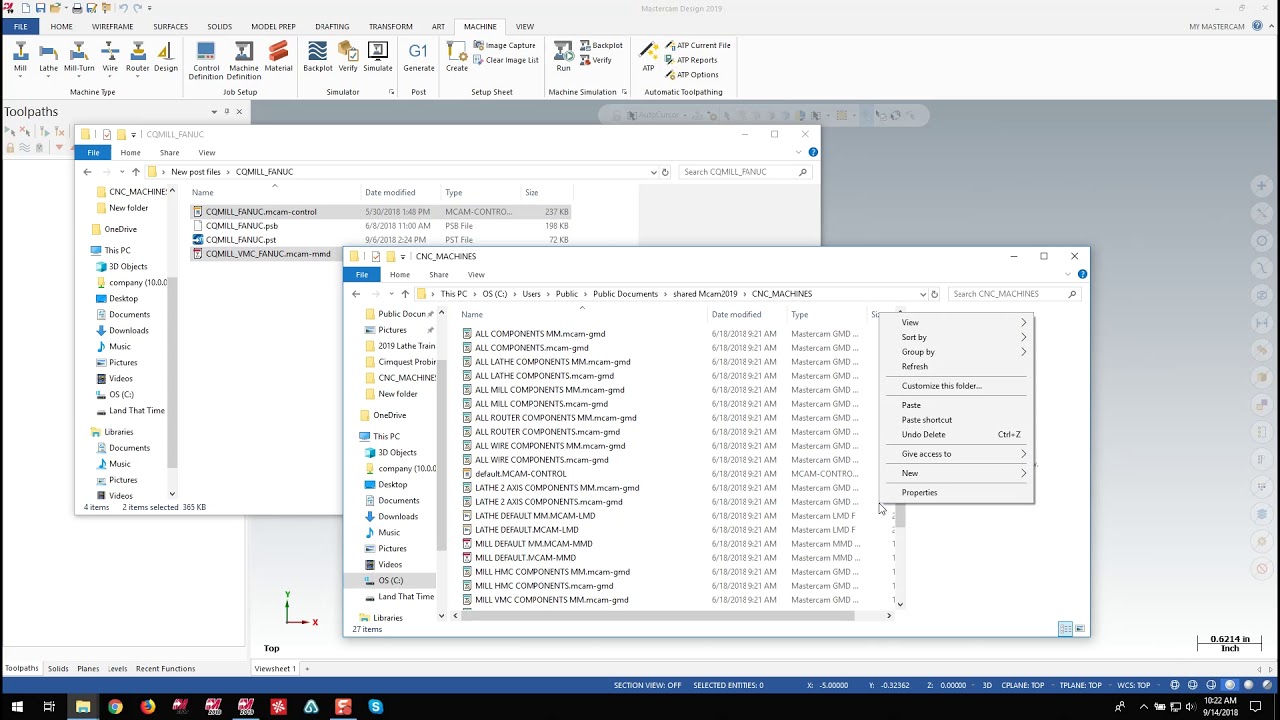
We were hitting the same issue with a new (to us) 5-axis CNC router that has a Fagor control. Maybe I'm missing something with tool offsets but I thought we had those Simulation parameters in the graphics screen are set correctly. Machine is zeroed with plenty of travel remaining in each axis, and the It always has to do with soft limits, even though our I just tried to run the attached sample program, and it read "1155 X axis Fagor told me that the postįrom autodesk for fagor was too "generic" after sending them a sample Those on the intelitek mill, but when I post process from inventor cam toįagor, they will not run on the fagor control. IĪlso can create post process for our intelitek mill in Inventor cam and run
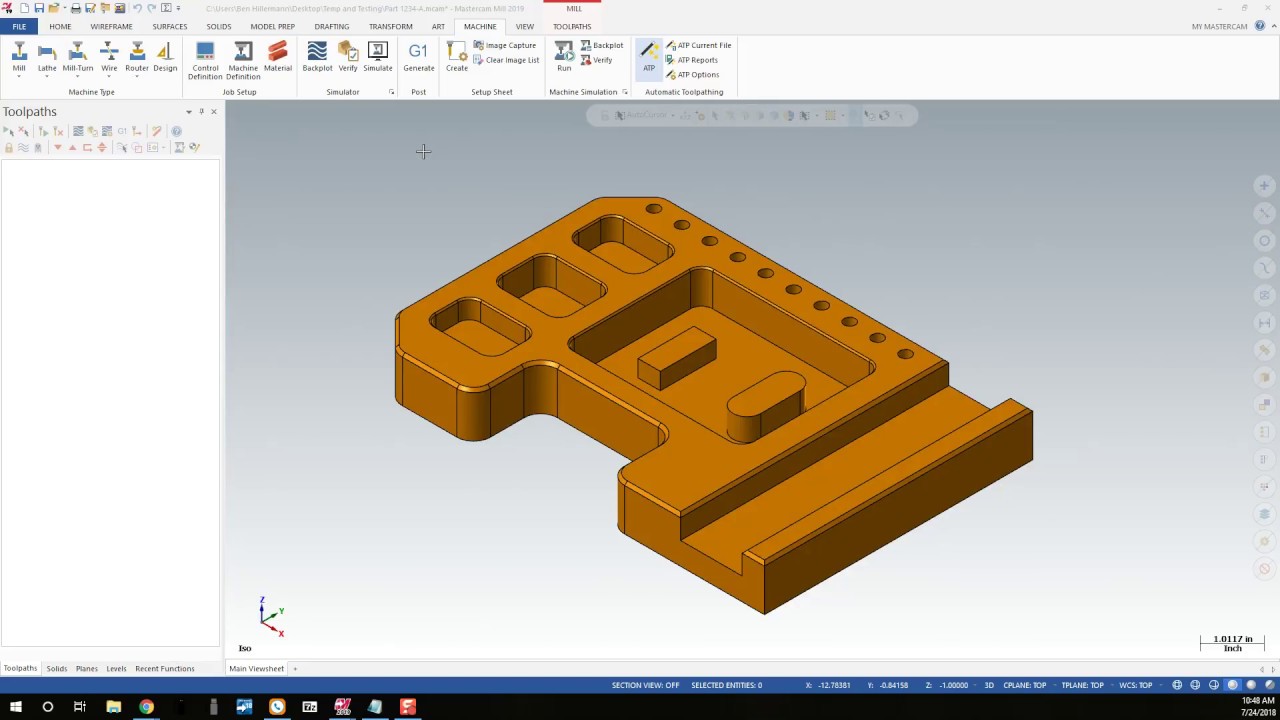
I have run programs on it that I typed in notepad and got them to work. Post processor such as mastercam or inventor cam. As far as sample programs, it was never tested with a program from a I tried to run the exact code you sent and it said "0004 No more yasnac sample of some posted code that Joshua submitted through support.siemens-840d error Danger of collision due to tool radius compensation 1.post-proccesor philips cnc 532 5 axis 1.Haas (pre-NGC) haas Post processor edit Help 1.
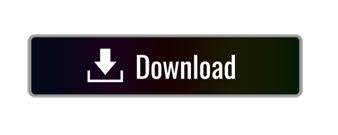